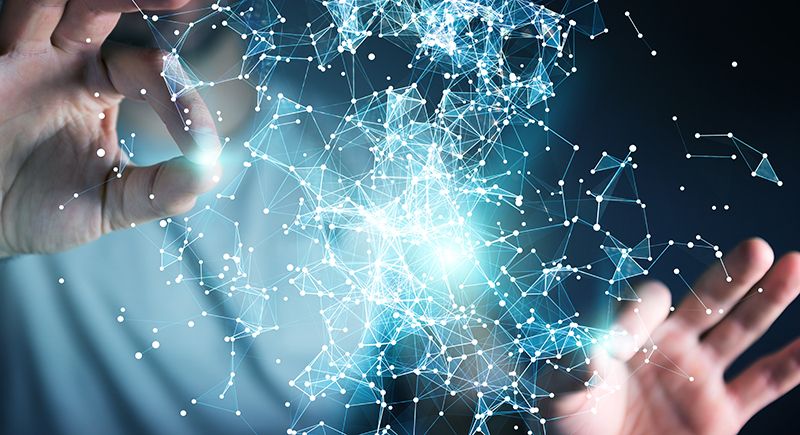
The price, quality or brand recognition have not been the only relevant factors in the pursuit of a competitive edge for a very long time now. The efficiency and the speed of a supply chain are becoming increasingly important. Developing companies put an ever-growing stress on the optimization of not just manufacturing or warehouse processes but also of the supply chain and, of course, the product distribution. It is in those areas that the fight against time is vital. While it is difficult for logistics specialists to speed up trucks that are on their way, they more and more often notice the possibility of streamlining processes by utilizing improvements in the communication with contractors, planning or delivery and shipment processing. Undoubtedly, the time spent on nailing down order details (be it via mail or on the phone), correcting and explaining errors resulting from such a form of communication or truck queues in front of warehouses is a TIME WASTED in a logistical chain!
A version of a future where transportation is dominated by unmanned vehicles is quite probable. A scenario where an internet-based shop sends off a drone right after a purchase (automatically and without a human intervention) to land on our lawn with the ordered product is also technologically feasible. However, before that happens, we can already use internet-based information systems for the speeding up of actions in the area of information exchange in real time or a more effective use of the resources of supply chain participants. This direction has seen not only a flow of logistical operators who include the optimization of YMS (yard management system) as a part of their job description but also manufacturers – no matter from what industry.
HOCHLAND – one of the largest cheese manufacturers and distributors in Europe – can serve as an example of a company that decided to implement a Yard Management System type app. The company has opted for the “Time Slots“ system supplied by LOGINTEGRA – a producer of logistics information solutions.
In retrospective, one could say that the amount of information exchanged between departments, companies and individual people is too high. On many occasions, matters important to us have drowned in the information noise directed to an incorrect or too numerous group of people. In the end, that took too much time and the generated message did not always reach all interested parties. We try to optimize processes used in a company, everywhere where it is possible. The change in the process of delivery and shipment servicing has enabled the implementation of systematics and distribute the warehouse workload accordingly to its capacity. In order to effectively make use of the notification system’s capability, it is important to understand its nature. The professional training provided by Logintegra is the deciding factor when it comes to an optimal implementation of the system. The implementation work has necessitated an increased integration of customer service, logistics, planning and purchasing, sales and warehouse departments in our two companies. Due to the integration, we could look at each part of the delivery and shipment process from a different perspective and understand their specifics and codependency that we have thus far failed to notice. At this time, every user has access to a knowledge repository regarding deliveries and shipments. The archiving enables storing of valuable for us information that can be helpful in the evaluation of our work as well as that of our suppliers and recipients. I think that the implementation of the notification system by Logintegra has enabled a higher degree of order in this process.
Adam Skrzypczak – Manager of a Warehouse Complex in Hochland Poland.